Solution to Over-fast Damage of Shale Shaker Screen
There are many main reasons for the quick breakage of mud shale shaker, such as unqualified shaker screen quality, tension of shaker screen, wrong steering of vibrating motor and accumulation of clay, which will lead to the quick breakage of mud shale shaker. In order to solve these problems, how should we avoid and make timely adjustments?
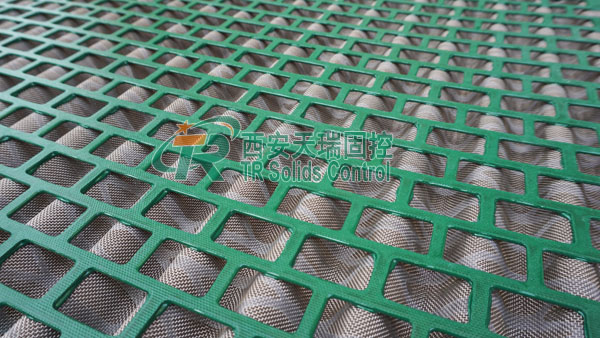
Shaker Screen tension is insufficient to cause screen tremor
Shaker Screen tension is insufficient to cause screen tremor
Shaker Screen tension is insufficient to cause screen tremor, which is usually broken or damaged along the edge of the screen or at the edge of the blanking press strip; screen quality is not up to standard, the screen generally has upper sieve stratification and lower stress layer, requiring that these two layers closely adhere to each other, if the pre-tensioning process is poor, when the bottom of the screen is subjected to.When the force layer is tightened, the layering of the screen is not tightened, and the throwing force of the drilling cuttings decreases greatly when the drilling cuttings are working, so that the drilling cuttings can not be discharged. When the vibration motor steering is wrong and vibration motor steering is debugged, the field operators consider that as long as the drilling cuttings go forward, the method is not suitable. Used for translating elliptical shaker.
The motor rotates inward incorrectly
If the motor rotates inward incorrectly, the projection angle is also forward, but the cuttings have the force of rolling backward. At this time, the speed of the cuttings moving forward is much slower. And the time spent on the screen is long, even the cuttings can not be discharged. How to effectively solve these problems: when the screen box is running, press the stop of the electronic control box.
At this time, the vibrating screen will stop slowly, observe the elliptical track formed by the small points on the side plate when the vibrating screen is running, roll to the sand outlet for correct turning; remove the shaker shield, check whether the apricot eccentric block rotates outward; change any two phase lines in the power supply of the electric control box, and sprinkle some sand on the screen. One of the quicker sand removal speeds is the right direction.
When drilling cuttings accumulate on the screen and quickly damage the screen, we should increase the vibration amplitude
- When drilling cuttings accumulate on the screen and quickly damage the screen, we should increase the vibration amplitude;
- Use spraying water to wash the screen and drilling cuttings to reduce the stickiness of the drilling cuttings, but this method is only suitable for situations where water is allowed to be added;
- Adjust the angle of the screen at the end of the sand outlet to downward, which is conducive to the discharge of cuttings by gravity, but may lead to slurry runoff;
- Changing the mesh number of screen or adjusting the flow rate of single screen to ensure that the flow stop point of drilling fluid is close to the outlet of screen, and drilling cuttings can be discharged smoothly under the lubrication of drilling fluid.
These are only part of the rapid breakage of the screen screen and the corresponding treatment methods. To solve this problem thoroughly, we need to have a shaker for mud. Maintenance, but also in time to find problems at work and give appropriate solutions.
Contact us
Sunny Lee | Sales manager
Leave a Reply