Replacement Derriok Screen to Argentina
An exciting news is coming from TR Solids Control, TR carefully built the replacement Derriok screen has been fully equipped to embark on the journey to Argentina, this very iconic move, not only highlights Tianrui’s deep heritage and strong strength in the screen manufacturing industry, It has also brought an excellent opportunity for many enterprises in Argentina to optimize screening operations and improve production efficiency, and has played a passionate movement for Tianrui to expand the international market and deepen global cooperation.
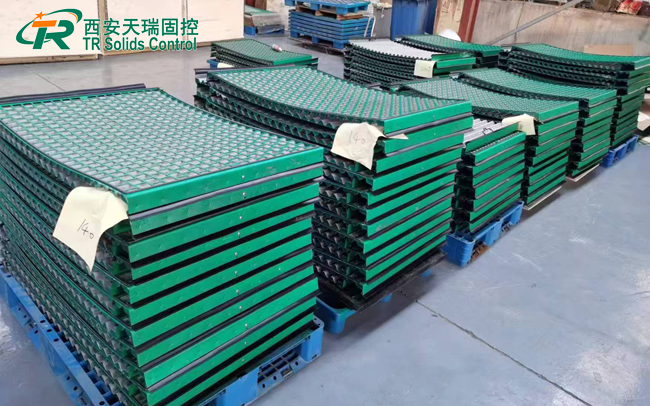
TR Solids Control as the authoritative brand in the field of screen manufacturing, with years of research and innovation in screening technology, as well as strict control of product quality, has already established an excellent reputation in the industry. The replacement Derriok screen specially created for the Argentine market is focused on solving the pain points of customers’ existing screening equipment, targeted multi-dimensional optimization and upgrading, which can be described as an innovative work with ingenuity and unique advantages.
This replacement Derriok screen, in the material selection of excellence, Tianrui R & D team scour the world’s high-quality raw materials, and finally selected a high strength, high toughness and excellent wear and corrosion resistance of the special alloy material, through advanced processing technology to create. This makes the screen in the face of various complex mining and industrial production environments in Argentina, can easily cope with frequent material impact and harsh chemical erosion, greatly extending the service life, for customers to effectively reduce the high cost and time loss caused by frequent screen replacement.
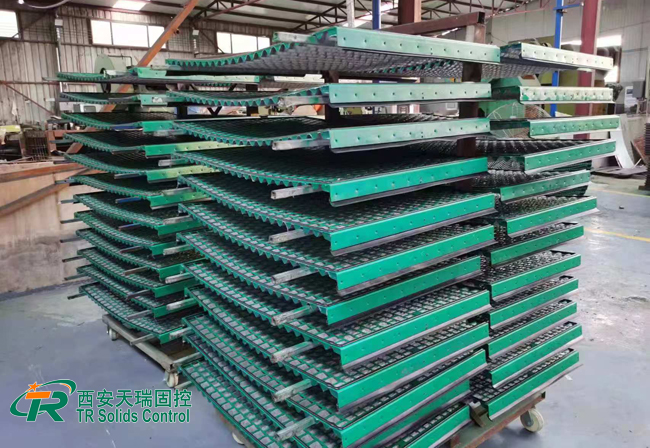
It is unique mesh design is a highlight. TR engineers used accurate computer simulation technology and rich practical experience to scientifically optimize the aperture, shape and arrangement of the mesh. This optimized mesh structure not only ensures the high precision of material screening, can accurately separate particles of different sizes, but also completely solves the traditional screen easy to block the problem, so that the flow of materials on the replacement Derriok screen is more smooth, screening efficiency compared with the traditional screen has been greatly improved, and then help the entire production process more efficient and stable operation.
It is worth mentioning that TR understands the importance of ease of installation for its customers and has taken this into account in the design of the replacement Derriok screen. It uses a highly versatile interface design, can perfectly adapt to all kinds of common screening equipment, customers do not need to carry out complex equipment transformation or debugging, you can easily complete the replacement of the screen installation work, minimize the equipment downtime, so that production can quickly return to normal, for the enterprise to gain valuable production time and economic benefits.
Argentina, as an important economy in South America, mining, construction, chemical and many other industries are booming, and the demand for high-quality screening equipment and replacement screens continues to grow. With its keen market insight, TR accurately captures this market demand, and with the excellent quality and excellent performance of its products, it successfully cooperates with many well-known companies in Argentina to provide them with tailor-made replacement Derriok screen solutions. This shipment is a key step in the implementation of these cooperation projects, and this batch of screens will be quickly put into the production line across Argentina, helping local enterprises to stand out in the fierce market competition and achieve the dual goal of reducing costs and increasing efficiency.
In order to ensure that this batch of replacement Derriok screen can arrive safely and on time in Argentina, TR Solids Control worked with professional international logistics giants to carefully prepare from the packaging process, using multiple layers of protective packaging materials to ensure that the screens are protected from collision, extrusion and any possible damage during long-distance transportation. At the same time, through the intelligent logistics tracking system, the whole process of cargo transportation is monitored in real time, so that customers can grasp the dynamics of the goods at any time, which fully reflects the service concept of Tianrui to customers.
The relevant person in charge of TR Solids Control expressed confidence: “We firmly believe that this replacement Derriok screen wholesale to Argentina will become the right hand of local enterprises in screening operations, with its excellent performance and reliable quality, to bring customers unprecedented screening experience.” This is also an important step for Tianrui to base itself on the global market and continue to expand its business. We will continue to adhere to the customer-centric concept, continue to develop and innovate, and provide more customers around the world with high-quality and efficient screen replacement products and a full range of service guarantees.”
Today, Tianrui’s replacement Derriok screen is carrying a lot of sincerity and expectations, across the ocean to Argentina. It is believed that in the near future, it will shine on the land of Argentina and become an indispensable part of the production line of many enterprises, and it will also further enhance the visibility and influence of Tianrui brand in the international market, attracting more international partners to open a new chapter in the field of screening with TR.
Are you still bothered by the frequent replacement of the existing screen and the low screening efficiency? Replacement Derriok screen is your best solution! Choose TR Solids Control, is to choose efficient, worry free, lasting screening guarantee, act quickly!
Buldhead Protector Double
The 16848-11 Buldhead Protector Double is engineered with advanced materials that offer superior protection against impacts and abrasions. It is design features double-layered construction. The double-layered construction significantly increases its durability and effectiveness in safeguarding the head.
The role in maintainingthe performance of hyperpool shakers is the 16848-11 Buldhead Protector Double. how it enhances the functionality of hyperpool shakers.
Understanding Hyperpool Shakers
Hyperpool shakers are vital in the drilling process. It is used to separate drilling fluids from cuttings. They ensure that the drilling operation remains efficient by recycling the drilling fluid. It is essential for maintaining pressure and cooling the drill bit. Given the harsh conditions under which these machines operate. It is crucial to equip them with high-quality 16848-11 Buldhead Protector.
The Role of the 16848-11 Buldhead Protector Double
The 16848-11 Buldhead Protector Double is specifically designed to provide enhanced protection for hyperpool shakers. This component acts as a barrier against the abrasive materials and harsh chemicals that are often present in drilling environments. The Buldhead Protector Double helps to prevent wear and tear, ultimately extending the lifespan of the equipment.
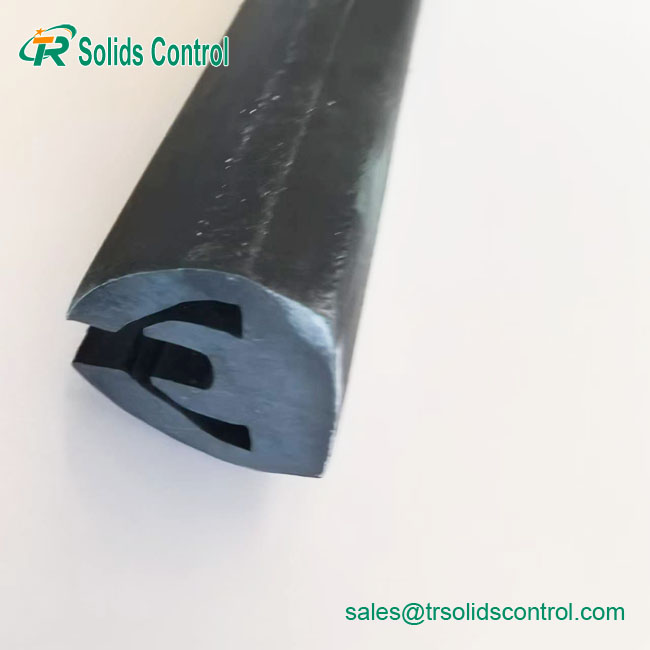
Key Features of the 16848-11 Buldhead Protector
1. Durability:
Constructed from high-quality materials, the 16848-11 Buldhead Protector Double is built to withstand extreme conditions. It is robust design ensures that it can handle the abrasive nature of drilling fluids and cuttings.
2. Easy Installation:
The design of the Buldhead Protector Double allows for straightforward installation on hyperpool shakers. This ease of installation minimizes downtime, enabling operators to quickly replace worn components and maintain operational efficiency.
3. Compatibility:
The 16848-11 Buldhead Protector Double is engineered to be compatible with various models of hyperpool shakers. This versatility makes it a preferred choice for many operators looking to enhance their equipment without the need for extensive modifications.
4. Cost-Effectiveness:
Investing in the Buldhead Protector Double can lead to significant cost savings in the long run. By reducing the frequency of repairs and replacements for the shaker. Operators can lower their maintenance costs and improve overall productivity.
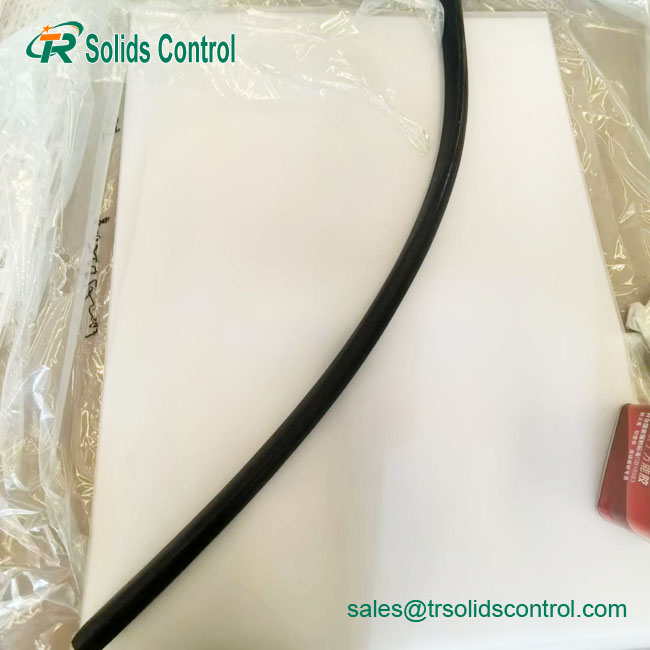
The integration of the 16848-11 Buldhead Protector into hyperpool shakers protects the machinery. By ensuring that the shaker operates at optimal performance levels, operators can achieve better separation of drilling fluids and cuttings. This improved efficiency translates to reduced waste and lower operational costs, making it a win-win for drilling operations.
The 16848-11 Buldhead Protector Double is an indispensable component for hyperpool shakers in the oil and gas industry. The importance of high-quality protective components like the Buldhead Protector Double will only grow. hyperpool shakers can meet the demands of modern drilling operations.
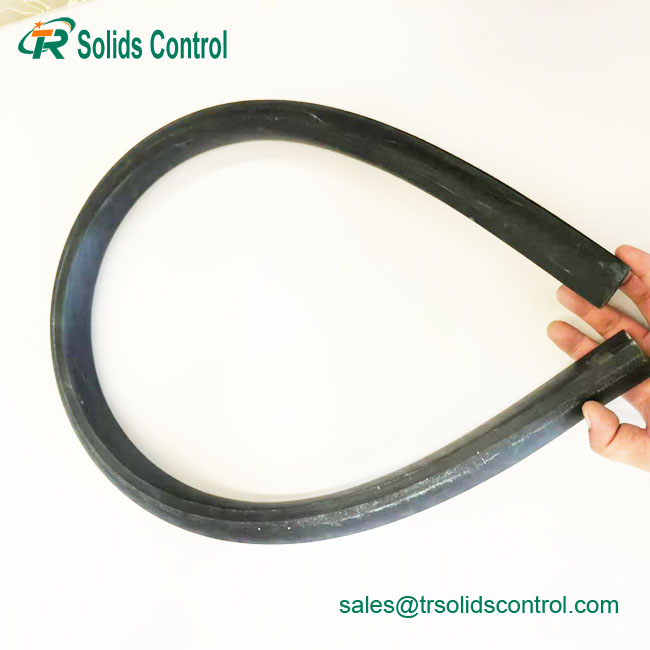
Contact us today to learn more about Side Support Rubber and shaker screens, how TR can support your solids control needs with innovative solutions.TR is a professional manufacturer for producing Solids Control System and Solids Control Equipment.If you need mud shale shaker, We will provide the high quality drilling shale shaker and best service. Your best Mud Recycling System start from TR solids control.
What Are The Best Shale Shaker Screens?
Best Shale shaker screen refers to the type of mechanical screen. It can separate solids and take them out from drilling fluid such as mud. Most shale shaker screens have stainless steel, composite, or polyurethane frame. The shale shaker has a moving or Best Shale shaker screen that removes cuttings from the mud for easy disposal. The vibrating sieve or screen can strain the cutting out of the mud. So, it plays a vital role before pumping the mud back into the borehole.
Shale shakers have become the easiest and most commonly used solids removal equipment. It can reduce costs during drilling applications. It comes in handy when you use a liquid as a drilling fluid. Circulate rate, drilling fluid properties, and shaker design control the screen selection. Unfortunately, when you use shale shakers incorrectly, the performance of the solid removal equipment falls down. Hence, you should choose the best shale shakers and use them properly. Read ahead to know more.
Benefits Of Shale Shaker Screen
While shale shaker has high significance, most people often overlook this piece of equipment. It has high importance on a drilling rig. The Best shale shaker screen acts as the first line of defense against major solids control equipment and drill cuttings. Shale shaker can ensure solids control. Therefore, it can ensure the following benefits:
- Increased drilling
- Lower disposal costs
- Reduced mud costs
- Enhanced bit life
Replacement SWACO Mongoose Composite Screen
The replacement SWACO Mongoose composite screen stands out for its innovative design and superior performance.This article delves into the features considerations of using replacement SWACO Mongoose composite screens in drilling applications.
Understanding SWACO Mongoose Composite Screen
The SWACO Mongoose composite screen is engineered to enhance the separation of solids from drilling fluids.SWACO Mongoose Composite Screen Made from a combination of composite materials.The screens offer a lightweight yet durable solution.The design of the Mongoose screen allows for optimal fluid flow while effectively capturing unwanted solids.
Features of SWACO Mongoose Composite Screen
- Durability.——The composite materials used in the construction of the Mongoose screens provide resistance to wear and tear. This durability translates to longer service life
- High Flow Capacity.——the SWACO Mongoose Composite Screen allows for a high flow rate, which is crucial in maintaining the efficiency of the drilling operation.
- Versatility.——Replacement SWACO Mongoose composite screens are compatible with various drilling fluids and can be used in different geological formations.This versatility makes them an ideal choice for a wide range of drilling applications.
- Easy Installation.——The design of the Mongoose screens facilitates quick and easy installation.This ease of use is a significant advantage in fast-paced drilling environments.
Benefits of Using Replacement SWACO Mongoose Composite Screen
The high flow capacity and effective solid separation capabilities of the Mongoose screens enhance the overall performance of the shale shaker. This improvement can lead to better drilling rates and increased productivity.
The replacement SWACO Mongoose composite screen is a vital component in modern drilling operations. The screens, operators can enhance their drilling performance. The importance of reliable like the Mongoose screen cannot be overstated.
We are an exporter of PWP shaker screen replacement.TR is a Derick Hyperpool screen maufuacturer and china Hyperpool screen supplier.Our factory approval the API,Drilling Shale Shakers and drilling PMD shaker screen have the API certification.TR solids control is the designed,selling,production,service and delivery of Chinese drilling fluid shakers manufacturers.We will provide the high quality shaker screen and swaco mongoose shaker screen.
Contact Us:TR Solids Control
Sales office:No.10 West of North 2nd Ring Road Xi’an City.
Manufacture: No.2 Goods yard road Xianyang City, Shaanxi Province.
Tel:+86-29-86332919
Call:18509252400
E-mail:sales@trsolidscontrol.com
PWP Shaker Screen Replacement
PWP shaker screen replacement have gained significant attention due to their durability and effectiveness.they require periodic replacement to maintain optimal performance.This article delves into the importance of PWP shaker screen replacement undertaking this task.

Understanding PWP Shaker Screen replacement
PWP shaker screen replacement are designed to separate solids from liquids in drilling fluids. These screens are made from a combination of 304, which provides them with enhanced strength and flexibility. Their unique design allows for improved separation efficiency, making them a preferred choice in various drilling applications.
PWP shaker screen replacement can wear out due to constant exposure to abrasive materials and harsh drilling conditions. A worn-out screen can lead to several issues, including:
- Reduced Efficiency
- Increased Wear on Equipment
- Poor Fluid Quality
PWP shaker screen replacement
When it comes to replacing PWP shaker screens, several factors should be taken into account:
- Screen Size and Type. Different drilling operations may require different screen sizes and types.It is crucial to select the right specifications to match the specific needs of your operation.
- Material Quality. Not all PWP screens are created equal.Opt for high-quality materials that can withstand the rigors of drilling operations.
- Manufacturer Reputation. Choose a reputable manufacturer known for producing reliable shaker screens.This can make a significant difference in the quality and performance of the screens.
- Installation and Maintenance.Proper installation is crucial for the effective functioning of shaker screens.
PWP shaker screen replacement is a vital aspect of maintaining efficiency and reliability in drilling operations.Investing in high-quality PWP shaker screens not only enhances performance but also contributes to the overall success of drilling operations.
We are an exporter of PWP shaker screen replacement.TR is a Derick Hyperpool screen maufuacturer and china Hyperpool screen supplier.Our factory approval the API,Drilling Shale Shakers and drilling PMD shaker screen have the API certification.TR solids control is the designed,selling,production,service and delivery of Chinese drilling fluid shakers manufacturers.We will provide the high quality shaker screen and swaco mongoose shaker screen.
Thanks for visiting our website. Please feel free to leave a message if you any questions.
Contact Us:TR Solids Control
Sales office:No.10 West of North 2nd Ring Road Xi’an City.
Manufacture: No.2 Goods yard road Xianyang City, Shaanxi Province.
Tel:+86-29-86332919
Call:18509252400
E-mail:sales@trsolidscontrol.com
Replacement PWP Shaker Screen
The Replacement PWP Shaker Screen distinguishes itself as a premier option that provides a multitude of advantages. Crafted with precision and care from high-quality materials. Replacement PWP Shaker screen ensures an extended service life,even under the most challenging operating conditions.It is engineered to endure heavy loads,making it a dependable choice for continuous operation.
This Replacement PWP Shaker Screen is designed to achieve outstanding separation efficiency. It effectively separates solid particles from liquids, ensuring a clean output while minimizing the risk of equipment damage. Its precise mesh size and configuration enhance optimal filtration capabilities, accommodating various particle sizes and types.
Replacement PWP Shaker Screen for Drilling Shaker
The Replacement PWP Shaker Screen exhibits compatibility with numerous shaker models.it can be seamlessly integrated into any solids control framework required in the field.
Installation of the Replacement PWP Shaker Screen is straightforward due to its user-centric design.It allows for quick replacement when necessary, thereby reducing downtime and enhancing productivity levels. This screen requires minimal effort for cleaning and maintenance tasks, resulting in lower overall ownership costs.
Despite its superior quality and performance characteristics, the Replacement PWP Shaker Screen offers an economical solution.it represents an excellent choice for effective solids control due to its exceptional quality combined with durable features that ensure superior separation performance.
We are an exporter of shaker screen.TR is a Derick Hyperpool screen maufuacturer and china Hyperpool screen supplier.Our factory approval the API,Drilling Shale Shakers and drilling PMD shaker screen have the API certification.TR solids control is the designed,selling,production,service and delivery of Chinese drilling fluid shakers manufacturers.We will provide the high quality shaker screen and swaco mongoose shaker screen.
Thanks for visiting our website. Please feel free to leave a message if you any questions.
Contact Us:TR Solids Control
Sales office:No.10 West of North 2nd Ring Road Xi’an City.
Manufacture: No.2 Goods yard road Xianyang City, Shaanxi Province.
Tel:+86-29-86332919
Call:18509252400
E-mail:sales@trsolidscontrol.com
FLC500 Shaker Screen
FLC500 Shaker Screen is meticulously engineered with precision and care. It is design stems from comprehensive research and advanced engineering expertise. The screen is made from high-quality materials that are durable and resistant to wear and tear. This ensures a long service life even in the harshest operating conditions.
FLC500 shaker screen smart design makes it easy to separate solids from liquids effectively.The mesh is set up for great filtration, letting only the right particles through while catching any solid bits. This not only improves the quality of the fluid being processed but also helps prevent damage to equipment from solid materials.
FLC500 Shaker Screen is designed to achieve a high level of separation efficiency. It can effectively remove even the smallest solid particles from the fluid, ensuring a clean and clear output. such as in oil and gas drilling, mining, and chemical processing.
FLC500 Shaker Screen is designed for easy maintenance. The screen can be easily removed and replaced, reducing downtime and maintenance costs.FLC500 Shaker Screen is suitable for a wide range of applications. It can be used in oil and gas drilling, where it helps to remove drill cuttings from drilling mud.
FLC500 Shaker Screen for Drilling
The FLC500 Shaker Screen is suitable for a wide range of applications. It can be used in oil and gas drilling, where it helps to remove drill cuttings from drilling mud.
When you choose the FLC500 Shaker Screen, you are choosing a product that is backed by a commitment to customer satisfaction. TR provides excellent after-sales service, including technical support and maintenance advice. This ensures that you get the most out of your investment and that your operations run smoothly and efficiently.
FLC500 Shaker Screen is a top-of-the-line product that offers precision, performance, and durability. you requires efficient solids control, the FLC500 is the perfect choice for your needs. Choose the FLC500 and experience the difference it can make in your operations.
We are an exporter of shale shaker screen.Our factory approval the API,Drilling Shale Shaker screens have the API certification.TR solids control is the designed,selling,production,service and delivery of Chinese drilling fluid shakers manufacturers.We will provide the high quality shaker screen.Your best shaker screen start from TR solids control.
Contact Us:TR Solids Control
Sales office:No.10 West of North 2nd Ring Road Xi’an City.
Manufacture: No.2 Goods yard road Xianyang City .
Tel:+86-29-86332919
Call:13186019379
E-mail:sales@trsolidscontrol.com
FLC514 Shaker Screen
In the realm of drilling and industrial processes that involve the management of fluids containing solid particles, possessing an efficient shaker screen is paramount. Introducing the FLC514 Shaker Screen, a product distinguished by its exceptional quality and performance.
I. Superior Design and Construction
The FLC514 Shaker Screen is meticulously engineered with precision and care. Its design stems from comprehensive research and advanced engineering expertise. Constructed from high-quality materials, it exhibits remarkable durability and resistance to wear, ensuring an extended service life even under the most challenging operating conditions.
The innovative construction of the FLC514 facilitates effective separation of solids from liquids. The mesh design is optimized for superior filtration, allowing only desired particles to pass through while effectively capturing solids. This not only enhances the quality of processed fluids but also mitigates potential equipment damage caused by solid particulates.
II. Enhanced Performance Features
High Separation Efficiency
The FLC514 Shaker Screen is specifically designed to achieve elevated levels of separation efficiency. It adeptly removes even minute solid particles from fluids, guaranteeing a clean output essential for applications where fluid purity is critical—such as in oil and gas drilling, mining operations, and chemical processing.
Easy Maintenance
Designed for user-friendly maintenance, the FLC514 allows for straightforward removal and replacement of screens—thereby minimizing downtime and maintenance costs. Additionally, its construction materials facilitate easy cleaning procedures that help maintain optimal screen condition over prolonged periods.
Stable Operation
This screen operates smoothly with minimal vibrations and noise levels, fostering a comfortable working environment while reducing risks associated with equipment failure due to excessive vibrations. The stable operation ensures consistent separation performance for reliable continuous operation.
The role of FLC514 Shaker Screen
III. Versatile Applications
The FLC514 Shaker Screen finds applicability across diverse sectors including oil and gas drilling—where it efficiently eliminates drill cuttings from drilling mud—as well as in mining operations for separating valuable minerals from waste rock; furthermore, it serves roles in chemical processing, wastewater treatment among other industries necessitating effective solids control solutions.
IV. Customer Satisfaction Guaranteed
By selecting the FLC514 Shaker Screen you are opting for a product backed by unwavering commitment to customer satisfaction; manufacturers provide exemplary after-sales support encompassing technical assistance along with maintenance guidance which ensures maximized investment returns alongside seamless operational efficiency.
The FLC514 Shaker Screen represents a premier solution offering precision engineering combined with outstanding performance characteristics coupled with durability; whether your focus lies within oil & gas exploration or mining—or any sector requiring proficient solids control—the FLC514 stands out as your ideal choice.
We are an exporter of shale shaker screen.Our factory approval the API,Drilling Shale Shaker screens have the API certification.TR solids control is the designed,selling,production,service and delivery of Chinese drilling fluid shakers manufacturers.We will provide the high quality shaker screen.Your best shaker screen start from TR solids control.
Contact Us:TR Solids Control
Sales office:No.10 West of North 2nd Ring Road Xi’an City.
Manufacture: No.2 Goods yard road Xianyang City .
Tel:+86-29-86332919
Call:13186019379
E-mail:sales@trsolidscontrol.com
Derrick Pyramid Screens
Derrick Pyramid screens has become a highly innovative and efficient solution. In both oil and gas drilling, effective solids control is critical.
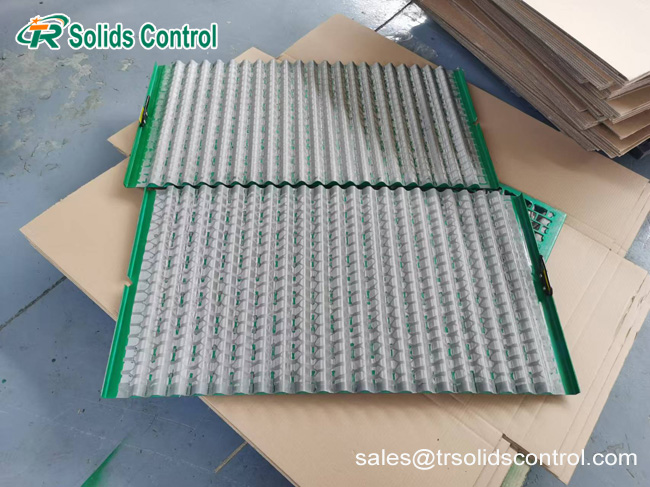
The role of Derrick Pyramid Screens
The pyramidal design of the Derrick Pyramid screens are not just for aesthetics. It provides a larger surface area than a traditional flat screen. The increased surface area allows for more efficient separation of solids from drilling fluids.
The shape of the Derrick pyramid screens also helps prevent clogging. When drilling mud passes through the shaker screen, solids are less likely to accumulate in one area because they are guided to the collection point by the pyramid’s slanted surface.
Derrick pyramid screens are constructed of high-grade materials. These materials have been carefully selected for their durability and ability to withstand the harsh conditions commonly found in drilling environments.
The pyramid screen design enables them to achieve higher separation efficiency. They can effectively remove solid particles of all sizes from drilling fluids, including very fine particles that are often difficult to separate.
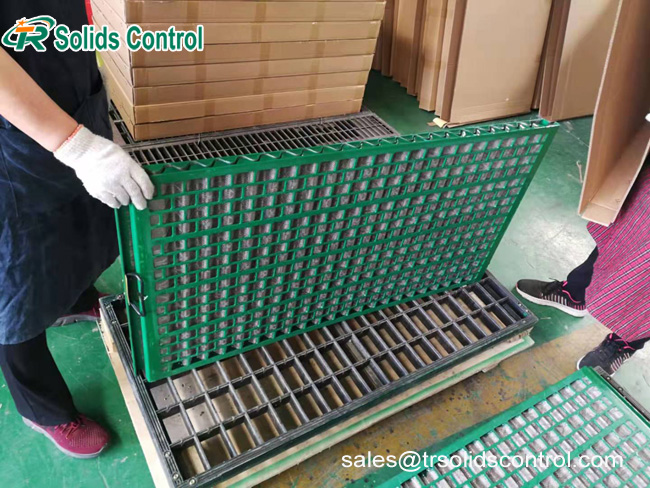
Due to its unique design, the derrick pyramid screens can handle larger volumes of drilling fluid compared to conventional screens. This increased capability is a significant advantage, especially in high-volume drilling operations where large volumes of fluids need to be handled quickly.
Our screens have passed the API13C test. We are also applying for API Q1 quality management certification. TR is a Derick Hyperpool screen maufuacturer and mud shale shaker supplier.
Derrick pyramid screens are a revolutionary technology in the field of drilling solid control. Its innovative design, high performance, cost performance, and applicability in a variety of drilling environments make it the first choice for drilling operators to optimize operations and improve overall efficiency.
hanks for visiting our website. Please feel free to leave a message if you any questions.
Contact Us:TR Solids Control
Sales office:No.10 West of North 2nd Ring Road Xi’an City.
Manufacture: No.2 Goods yard road Xianyang City, Shaanxi Province.
Tel:+86-29-86332919
Call:18509252400
E-mail:sales@trsolidscontrol.com
Polyurethane Screen
Polyurethane screen mesh stands out as a game-changer. Are you looking for a reliable and efficient screening solution? Look no further than Polyurethane screen mesh.
Polyurethane screen mesh is crafted with precision and innovation. It offers a host of benefits that make it the ideal choice for a wide range of applications.
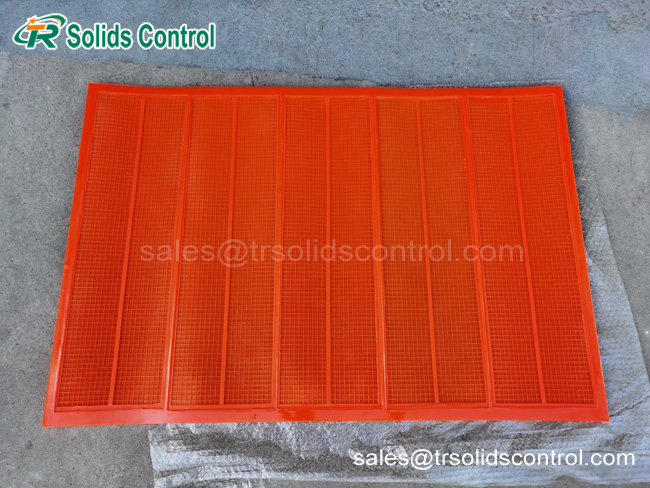
One of the key advantages of Polyurethane screen mesh is its exceptional durability. Made from high-quality polyurethane materials, it can withstand the harshest of operating conditions. Whether it’s abrasive materials, high-impact forces, or extreme temperatures, this screen mesh holds up remarkably well. This means less downtime for maintenance and replacement, saving you time and money in the long run.
The unique design of Polyurethane screen mesh also provides excellent screening efficiency. With its precise mesh openings, it accurately separates materials of different sizes, ensuring a clean and accurate output. This is crucial for industries that demand high-quality separation, such as mining, quarrying, and aggregate processing.
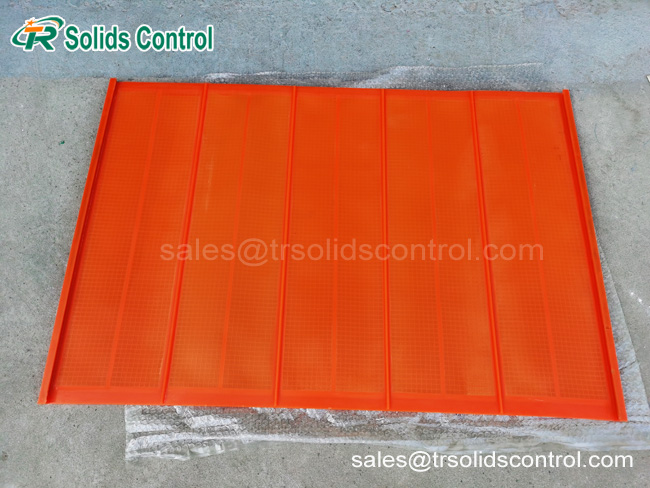
More over, Polyurethane screen mesh is highly resistant to clogging. Its smooth surface and flexible nature prevent materials from sticking, ensuring a continuous flow of materials through the screen. This not only improves productivity but also reduces the need for frequent cleaning and maintenance.
In addition to its practical benefits, Polyurethane screen mesh is also environmentally friendly. It is recyclable, reducing waste and minimizing the impact on the environment. This makes it a sustainable choice for businesses that are committed to environmental responsibility.
Our Polyurethane screen mesh comes in a variety of sizes and specifications to meet your specific needs. Whether you need a fine mesh for detailed separation or a coarse mesh for larger materials, we have the perfect solution for you.
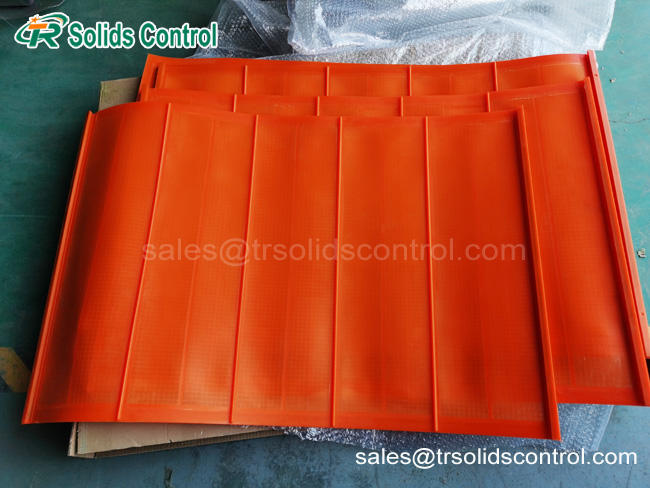
Polyurethane screen Supplier
More over, Polyurethane screen mesh is highly resistant to clogging. Its smooth surface and flexible nature prevent materials from sticking, ensuring a continuous flow of materials through the screen. This not only improves productivity but also reduces the need for frequent cleaning and maintenance.
In addition to its practical benefits, Polyurethane screen mesh is also environmentally friendly. It is recyclable, reducing waste and minimizing the impact on the environment. This makes it a sustainable choice for businesses that are committed to environmental responsibility.
Our Polyurethane screen mesh comes in a variety of sizes and specifications to meet your specific needs. Whether you need a fine mesh for detailed separation or a coarse mesh for larger materials, we have the perfect solution for you.
TR is dedicated to providing top-quality Polyurethane screen mesh and exceptional customer service. Our team of experts is always ready to assist you in choosing the right product for your application and answer any questions you may have.
Don’t settle for inferior screening solutions. Choose Polyurethane screen mesh and experience the difference it can make in your operations. Contact us today and let us help you take your screening process to the next level.
We are an exporter of shaker screen.TR is a Derick Hyperpool screen maufuacturer and china Hyperpool screen supplier.Our factory approval the API,Drilling Shale Shakers and drilling PMD shaker screen have the API certification.TR solids control is the designed,selling,production,service and delivery of Chinese drilling fluid shakers manufacturers.We will provide the high quality shaker screen and swaco mongoose shaker screen.
Thanks for visiting our website. Please feel free to leave a message if you any questions.
Contact Us:TR Solids Control
Sales office:No.10 West of North 2nd Ring Road Xi’an City.
Manufacture: No.2 Goods yard road Xianyang City, Shaanxi Province.
Tel:+86-29-86332919
Call:18509252400
E-mail:sales@trsolidscontrol.com
Web:www.solidscontrolequipment.com
www.trsolidscontrol.com